Your cart is currently empty!
Author: Linda Janet Tivane
SayPro is a Global Solutions Provider working with Individuals, Governments, Corporate Businesses, Municipalities, International Institutions. SayPro works across various Industries, Sectors providing wide range of solutions.
Email: info@saypro.online Call/WhatsApp: Use Chat Button 👇
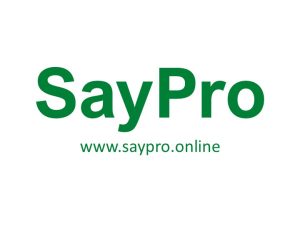
SayPro Course Setup Ensure all tools and materials are stocked and ready for practical sessions.
SayPro Course Setup: Ensuring All Tools and Materials are Stocked and Ready for Practical Sessions
One of the key components of an effective SayPro Sheet Metal Fabrication Program is the availability of the right tools and materials for hands-on training. Ensuring that these resources are stocked and ready before practical sessions not only maximizes student learning but also maintains safety and operational efficiency in the workshop.
Here is a step-by-step guide to ensure all tools and materials are prepared for practical sessions.
1. Inventory Check and Tool Readiness
Tasks:
- Conduct an Inventory Assessment: Review and update the list of tools and materials required for each practical session (e.g., cutting tools, welding machines, bending presses).
- Identify Essential Tools: Ensure that all tools critical to the hands-on experience are available in sufficient quantity (e.g., shears, press brakes, welding torches).
- Check Tool Condition: Inspect all tools for wear and tear. Ensure that they are in good working condition and free from defects. If any tools are damaged, schedule repairs or replacements.
- Stock Necessary Consumables: Ensure that consumables like welding rods, cutting discs, sanding paper, clamps, and PPE (Personal Protective Equipment) are stocked in the right quantities.
- Safety Equipment: Verify that there is a sufficient amount of safety gear (e.g., gloves, goggles, helmets, aprons, ear protection) for each student.
Example Items to Check:
- Cutting Tools: Plasma cutters, shears, angle grinders.
- Welding Equipment: MIG welders, TIG welders, welding rods, wire spools.
- Measuring Tools: Calipers, micrometers, measuring tapes, and squares.
- Bending Equipment: Bending presses, manual and powered benders.
- Workbenches and Clamps: Ensure that benches are sturdy, with sufficient clamps and supports for workpieces.
2. Tool Calibration and Setup
Before any practical session, ensure that all equipment is properly calibrated and set up for use. This step ensures accuracy and safety during training.
Tasks:
- Calibrate Equipment: Ensure that machines and tools are properly calibrated to meet industry standards. This includes checking cutting precision, welding heat settings, and tool alignment.
- Set Up Stations: Prepare workstations with the necessary equipment for each student or group. Ensure that each station has the proper tools and enough space for students to work comfortably and safely.
- Test Equipment: Run a test session on each piece of equipment (e.g., testing the welding machines, cutting machines, and presses) to verify that they are functioning as expected.
3. Materials and Supplies Preparation
In addition to the tools, you must ensure that the necessary materials are stocked and ready for use during the practical training sessions.
Tasks:
- Material Selection: Identify and stock the required metals and materials for each practical session. For example, if the session focuses on cutting metal sheets, ensure you have sufficient steel sheets of various gauges.
- Types of Metals: Stock a variety of metals used in sheet metal fabrication, including mild steel, aluminum, stainless steel, and copper.
- Variety of Thicknesses: Ensure a range of material thicknesses to allow students to practice with different levels of difficulty.
- Specialized Materials: If the course includes more advanced topics, ensure that specialized materials (e.g., high-strength alloys or composite materials) are available.
- Ensure Adequate Quantity: Check that there is enough material for each student to complete their tasks without interruption. Keep extra stock for errors or material waste.
- Pre-Cut and Prepared Materials: If certain materials need to be pre-cut or prepared (e.g., pre-cut metal sheets for welding or bending), ensure these tasks are done before the practical session begins.
4. Safety Gear and PPE
Safety is paramount in sheet metal fabrication. Ensure that each student has access to the appropriate Personal Protective Equipment (PPE) during all practical sessions.
Tasks:
- Inspect Safety Gear: Verify that all PPE is in good condition and available in sufficient quantities. This includes:
- Welding Gloves: Ensure they are heat-resistant and free of damage.
- Protective Eyewear: Safety goggles or face shields to protect from sparks and debris.
- Welding Helmets: Ensure helmets are in good working condition with auto-darkening lenses.
- Aprons: Ensure students have durable, heat-resistant aprons.
- Ear Protection: Stock earplugs or earmuffs to protect from noise exposure during cutting or welding.
- Replace Damaged PPE: Regularly check for wear and tear, and replace any damaged or worn-out equipment promptly.
5. Workshop Organization and Cleanliness
A clean and well-organized workshop promotes safety and efficiency. Ensure that all tools, materials, and equipment are organized and easy to access.
Tasks:
- Organize Tool Stations: Ensure that each station is clearly labeled and well-organized. Group tools by type (e.g., cutting tools, welding equipment, measuring tools) for easy access.
- Cleaning Protocol: Establish a routine for cleaning tools and equipment after use. This includes wiping down machines, cleaning workbenches, and organizing any leftover materials.
- Hazardous Waste Disposal: Ensure proper disposal of any hazardous materials, such as welding rods, metal filings, and chemicals used in the fabrication process. Provide clearly labeled bins for these items.
6. Final Check and Pre-Course Setup
Before the course begins, conduct a final walk-through of the workshop to ensure everything is ready for use.
Tasks:
- Final Tool Check: Perform a last-minute inspection to ensure that tools are clean, calibrated, and in working order.
- Materials Check: Verify that there is enough material for the first lesson, and confirm that it is easily accessible.
- Emergency Equipment: Ensure that first aid kits are stocked and fire extinguishers are fully charged and accessible.
- Clear Workspaces: Ensure that there is no clutter in the workstations and that each student has enough space to perform their tasks safely.
- Instructor Preparedness: Confirm that instructors have all the necessary teaching materials, such as lesson plans, safety guidelines, and any checklists for monitoring student progress.
7. Monitoring During the Course
Once the course has started, it’s important to continue monitoring the availability of tools and materials throughout the practical sessions.
Tasks:
- Tool Usage Tracking: Monitor how often tools are being used and if any need maintenance during the session. This prevents unexpected downtime due to broken equipment.
- Material Usage: Keep track of material consumption, and ensure students don’t run out of supplies during the lesson.
- Stock Replenishment: Keep a close eye on stock levels, and reorder tools, materials, and consumables as necessary during the course.
8. Post-Course Review
At the end of each course, conduct an assessment to evaluate the efficiency of the tools and materials used during the sessions.
Tasks:
- Feedback from Instructors: Have instructors provide feedback on whether the tools and materials were adequate for the lessons.
- Student Feedback: Gather student feedback to determine if any tools or materials were lacking or difficult to use.
- Post-Course Inventory: Check inventory levels and prepare to reorder any tools or materials that were used during the course.
Conclusion
Ensuring that all tools and materials are stocked and ready for practical sessions is essential for the success of the SayPro Sheet Metal Fabrication Program. Proper planning, inventory management, and safety checks will help facilitate smooth, effective learning and create a safe environment for students. By implementing these steps, you can be confident that the course will run efficiently and that students will have everything they need to succeed in their practical training.
- Conduct an Inventory Assessment: Review and update the list of tools and materials required for each practical session (e.g., cutting tools, welding machines, bending presses).
SayPro Course Setup: Develop and finalize the course curriculum for the upcoming quarter.
SayPro Course Setup: Development and Finalization of the Course Curriculum for the Upcoming Quarter
To ensure a successful and efficient SayPro Sheet Metal Fabrication Program for the upcoming quarter, it’s crucial to develop and finalize a comprehensive course curriculum that aligns with industry standards, learning objectives, and student needs. This curriculum should be well-structured to provide both theoretical knowledge and practical skills while maintaining a focus on safety, industry relevance, and student engagement.
Below is a step-by-step approach to developing and finalizing the curriculum for the upcoming quarter.
1. Review of Previous Quarter (Evaluation and Improvement)
Before creating the new curriculum, it’s important to evaluate the previous quarter’s course to determine what worked well and what areas can be improved. Gather feedback from instructors and students to identify areas for improvement in course content, delivery, and materials.
Tasks:
- Review Student Feedback: Analyze survey results or informal feedback from students on the effectiveness of the previous course.
- Instructor Feedback: Have instructors provide insights on course material, student engagement, and any challenges faced.
- Assess Student Performance: Evaluate the overall performance of students (e.g., grades, skills assessments) to identify which areas may need more focus.
- Identify Improvements: Based on feedback, identify any adjustments to the curriculum, such as content updates, additional lessons, or enhanced teaching methods.
2. Defining Course Objectives and Learning Outcomes
The core of any curriculum is its objectives and learning outcomes, which should be measurable, specific, and aligned with the industry standards. These will guide the structure and delivery of the course.
Tasks:
- Define Core Competencies: Outline the key skills and knowledge that students must master by the end of the course (e.g., cutting, welding, bending, safety protocols).
- Theoretical Knowledge: Specify the theoretical aspects of the course, such as understanding metal properties, fabrication processes, and safety standards.
- Practical Application: Ensure students will have hands-on experience with tools, machinery, and techniques used in sheet metal fabrication.
- Safety Knowledge: Emphasize the importance of personal protective equipment (PPE), tool handling, and emergency procedures.
Example Learning Outcomes:
- Students will be able to cut and shape metal with precision using industry-standard tools.
- Students will demonstrate proficiency in welding techniques, including MIG and TIG welding.
- Students will understand metal properties and how they affect fabrication processes.
- Students will identify and apply safety protocols in a workshop environment.
3. Structuring the Course Content
The course should be broken down into modules or units that cover both theory and practical skills. Each module should have specific objectives, lesson plans, and assessment criteria.
Tasks:
- Course Outline: Create a structured outline of the course, breaking it down into units or modules (e.g., Introduction to Sheet Metal Fabrication, Welding Techniques, Cutting and Bending Metal, Blueprint Reading, etc.).
- Lesson Plans: Develop detailed lesson plans for each module. Include key teaching points, hands-on activities, resources required (e.g., tools, machines), and any supplementary materials (e.g., videos, reading materials).
- Assessment Methods: Determine how each module will be assessed. Will it be through practical exams, written tests, project work, or a combination of these?
- Time Allocation: Allocate a specific number of hours to each module (e.g., 2 hours of theory, 4 hours of hands-on practice, 1 hour of assessment).
Example Course Structure:
- Introduction to Sheet Metal Fabrication (Week 1)
- Overview of sheet metal fabrication and its applications.
- Safety protocols and PPE.
- Hands-on activity: Introduction to tools (cutting, bending, welding).
- Welding Techniques (Week 2-3)
- Overview of welding processes (MIG, TIG, Stick welding).
- Hands-on: Welding practice (joint formation, penetration, and control).
- Metal Cutting and Shaping (Week 4)
- Types of cutting methods (shearing, plasma cutting, laser cutting).
- Hands-on practice with cutting tools and machines.
- Blueprint Reading and Design (Week 5)
- Introduction to technical drawings and symbols.
- Understanding fabrication plans.
- Hands-on project: Create and follow a fabrication blueprint.
4. Aligning with Industry Standards and Best Practices
To ensure that the curriculum is relevant to the current industry needs, it’s essential to incorporate industry practices, tools, and techniques that are commonly used in the field.
Tasks:
- Consult Industry Experts: Collaborate with industry professionals to ensure the curriculum meets the current standards and demands.
- Research Industry Trends: Stay up to date with the latest developments in sheet metal fabrication (e.g., new tools, machinery, or materials).
- Update Curriculum Content: Revise the curriculum to include the latest tools, technologies, and best practices in the industry.
- Incorporate Safety Best Practices: Review and update the safety standards in line with the latest regulations (e.g., OSHA standards, ISO certifications).
5. Preparing Course Materials
Once the structure of the course is finalized, it’s time to prepare the course materials, which should be designed to support both theoretical and practical learning.
Tasks:
- Textbooks/Reading Materials: Select textbooks, articles, and other reading materials that align with the course content.
- Handouts and Worksheets: Create handouts or worksheets for students to follow during practical lessons or take home for review.
- Presentation Slides: Develop slides to aid in theoretical lessons (e.g., PowerPoint presentations on metal properties or welding processes).
- Videos/Interactive Content: Consider creating or sourcing instructional videos that show key techniques, tool operation, or safety measures.
- Assessments: Prepare assessments for the course, including quizzes, practical exams, and projects.
6. Instructor and Student Readiness
Tasks:
- Instructor Training: Ensure instructors are prepared by providing them with the finalized curriculum, teaching materials, and any necessary updates (e.g., new safety procedures, equipment usage).
- Student Orientation: Provide students with an orientation session at the beginning of the course, explaining the structure, expectations, and resources available to them.
- Tool and Equipment Check: Ensure that all tools and equipment are in working order before the start of the course (e.g., cutting tools, welding machines).
7. Finalizing the Curriculum
Once all components have been developed, finalize the curriculum and ensure it’s ready for implementation.
Tasks:
- Approval Process: Have the curriculum reviewed and approved by relevant stakeholders (e.g., department heads, safety officers).
- Course Schedule: Finalize the course schedule, ensuring that it includes enough time for practical sessions, theory, assessments, and breaks.
- Distribution: Distribute the curriculum and course materials to all instructors and students before the first session.
8. Monitor and Review Throughout the Quarter
Once the course begins, continuous monitoring is important to ensure it is being delivered effectively.
Tasks:
- Ongoing Feedback: Gather feedback from students and instructors throughout the quarter to make any necessary adjustments to the course.
- Mid-Course Check-In: Hold a meeting or survey with students mid-way through the course to assess their progress and gather any concerns.
Conclusion
The SayPro Course Setup for the upcoming quarter involves careful planning, development, and finalization of the course curriculum to ensure students gain both theoretical knowledge and hands-on experience in sheet metal fabrication. By structuring the course effectively, aligning with industry standards, and ensuring proper preparation for instructors and students, the course can provide a high-quality learning experience that prepares students for successful careers in the industry.
SayPro Safety Incident Reports: If any safety incidents occur, these should be documented and reviewed.
SayPro Safety Incident Reports: Documentation and Review of Safety Incidents
In the SayPro Sheet Metal Fabrication Program, ensuring a safe working environment is of utmost importance. Any safety incidents, whether minor or major, must be documented and reviewed to prevent recurrence and to ensure proper corrective actions are taken. Safety Incident Reports provide a structured approach to tracking, analyzing, and addressing safety-related issues.
1. Purpose of Safety Incident Reports
- Ensure Accountability: Proper documentation ensures that all safety incidents are tracked and that responsible parties are identified.
- Prevent Future Incidents: By analyzing incidents and implementing corrective actions, the likelihood of similar events occurring in the future can be reduced.
- Legal and Compliance Requirements: In many cases, documentation of safety incidents is required for compliance with safety regulations and standards.
- Employee Well-being: Ensures that corrective measures are taken to protect students and instructors, fostering a safe training environment.
2. Key Components of a Safety Incident Report
Each Safety Incident Report should capture comprehensive details of the incident, including context, action taken, and follow-up measures. Below are the essential components to include in the report:
a. Incident Details
- Incident ID: A unique identifier for the incident for easy tracking and reference.
- Date and Time of Incident: When the incident occurred.
- Location: The specific location in the workshop where the incident took place.
- Type of Incident: Categorize the incident (e.g., Injury, Near Miss, Property Damage, Equipment Malfunction).
- Equipment Involved: Identify any equipment or tools involved (e.g., CNC Machine, Welding Torch).
b. People Involved
- Injured or Affected Individual(s): Name(s) of the person(s) affected by the incident, including students, instructors, or other staff.
- Witnesses: Names of any witnesses who saw the incident occur.
- Instructor/Responder: Name of the instructor or staff member who responded to the incident.
- Role: The role of each individual involved (e.g., student, instructor, technician).
c. Description of Incident
- Incident Narrative: A detailed, factual description of what happened leading up to the incident. This should include:
- What the person was doing at the time of the incident (e.g., cutting metal, welding, adjusting equipment).
- Any factors that contributed to the incident (e.g., failure to follow safety protocols, equipment malfunction, environmental conditions).
- Whether the incident involved equipment, environmental hazards, or human error.
- Immediate Actions Taken: The actions that were taken right after the incident occurred (e.g., first aid administered, emergency services called, equipment shut down).
d. Injury or Damage
- Nature of Injury: If the incident involved injury, describe the type and severity (e.g., minor burn, laceration, fracture).
- Treatment Given: Medical treatment provided (e.g., first aid, hospital visit).
- Property or Equipment Damage: Describe any damage to equipment or property (e.g., broken welding torch, damaged workbench).
e. Root Cause Analysis
- Investigation Findings: A brief summary of the investigation, including any discovered root causes or contributing factors (e.g., faulty equipment, lack of PPE, improper training).
- Corrective Actions: Any immediate actions taken to fix or mitigate the issue (e.g., repairing faulty equipment, increased safety training).
- Long-Term Preventive Measures: Actions to prevent a recurrence of the incident (e.g., updating safety protocols, replacing damaged equipment, increased supervision during critical tasks).
f. Safety Follow-Up Actions
- Follow-Up Review: Details of any follow-up actions required or recommended (e.g., monitoring equipment performance, additional training for involved individuals).
- Safety Improvements: Any proposed or implemented changes to safety procedures or equipment after the incident (e.g., new PPE requirements, adjustments to equipment maintenance schedules).
g. Incident Report Review
- Reviewed By: The name(s) of the person(s) who reviewed the incident and report (e.g., Safety Officer, Workshop Supervisor).
- Date of Review: The date the report was reviewed and finalized.
- Follow-Up Meeting: Whether a meeting was held to discuss the incident with the involved parties and how to prevent similar incidents.
3. Example of a Safety Incident Report
Field Details Incident ID SI-2025-001 Date and Time of Incident 2025-03-25, 10:30 AM Location Workshop 3, Sheet Metal Fabrication Station Type of Incident Injury (Minor Burn) Equipment Involved MIG Welder People Involved Jane Smith (Student), John Doe (Instructor) Witnesses Mark Johnson (Student), Sarah Lee (Instructor) Instructor/Responder John Doe (Instructor) Description of Incident Jane was welding a metal sheet when the welding torch malfunctioned, causing a small flame to burn her glove. She immediately extinguished the flame, but suffered a minor burn on her hand. Immediate Actions Taken Instructor John Doe applied first aid, and Jane was escorted to the first aid kit. No medical assistance was needed, but the equipment was shut down for inspection. Nature of Injury Minor burn on left hand (second-degree burn). Treatment Given First aid (cooling burn, bandaging). Property or Equipment Damage No property or equipment damage. Root Cause Analysis Investigation revealed that the welding torch had a small gas leak, which caused the unexpected flame. Additionally, Jane had not checked the torch for proper operation before use. Corrective Actions Torch was immediately repaired. Jane received additional training on equipment checks. Long-Term Preventive Measures All welding equipment will undergo regular safety checks, and a new protocol will be introduced to ensure proper equipment inspection before use. Follow-Up Review Safety review scheduled for 2025-04-01 with all welding students. Reviewed By Sarah Lee (Workshop Supervisor) Date of Review 2025-03-26 Follow-Up Meeting Yes, to discuss equipment checks and additional safety training. 4. How to Maintain and Use Safety Incident Reports
a. Record Keeping
- Digital Logs: Store all incident reports in a centralized database or cloud-based document management system. This ensures easy retrieval and access for safety reviews and audits.
- Physical Copies: Keep hard copies of safety incident reports in a safety logbook or incident binder if necessary for compliance or regulatory purposes.
b. Regular Reviews
- Safety Meetings: Safety incidents should be reviewed regularly in safety meetings to discuss preventive measures, safety improvements, and lessons learned.
- Trend Analysis: Regularly analyze incident reports to identify patterns or recurring issues (e.g., if certain equipment is involved in multiple incidents).
c. Staff and Student Involvement
- Instructor Training: Ensure that all instructors are trained on how to properly handle and document safety incidents.
- Student Awareness: Educate students on the importance of reporting incidents, near misses, and unsafe conditions, and how they should respond in case of an emergency.
5. Benefits of Safety Incident Reports
- Prevention: Helps identify and address risks before they result in serious accidents or injuries.
- Compliance: Ensures compliance with workplace safety regulations, including record-keeping and reporting standards.
- Accountability: Establishes clear accountability for safety procedures and the actions taken in response to incidents.
- Continuous Improvement: Provides valuable insights into areas where safety practices can be improved, leading to a safer learning environment.
Conclusion
SayPro Safety Incident Reports are a critical component of a strong safety management system in the Sheet Metal Fabrication Program. By documenting each safety incident thoroughly and taking corrective actions, SayPro ensures that safety remains a top priority, helping to maintain a safe environment for both students and instructors. If you need further assistance or templates for safety incident reporting, feel free to ask!
SayPro Student Progress Reports: Documentation of student performance, including skill assessments and feedback.
SayPro Student Progress Reports: Documentation of Student Performance
To ensure that students in the SayPro Sheet Metal Fabrication Program are meeting the necessary standards and receiving the support they need to succeed, it’s important to maintain comprehensive Student Progress Reports. These reports document each student’s performance across both practical skills and theoretical knowledge, as well as providing feedback on their strengths and areas for improvement.
1. Purpose of Student Progress Reports
- Track Student Development: Helps instructors and students monitor progress over time and identify strengths and areas where additional focus is needed.
- Provide Constructive Feedback: Offers feedback to guide students in improving their skills, knowledge, and safety practices.
- Evaluate Skill Mastery: Ensures students meet specific skill benchmarks, including both technical competencies (e.g., welding, cutting) and theoretical understanding (e.g., metal properties, fabrication processes).
- Documentation for Certification: Provides official records required for issuing certifications, graduation, or employment verification.
2. Key Components of a Student Progress Report
Each Student Progress Report should contain detailed, structured information about the student’s skills, knowledge, and overall performance. Below are the key components of the report:
a. Student Information
- Student Name: Full name of the student.
- Student ID: Unique identification number assigned to the student.
- Course Name/ID: Name of the course or module the student is enrolled in (e.g., “Sheet Metal Fabrication 101”).
- Instructor Name: Name of the instructor responsible for evaluating the student.
- Report Date: The date the report is created or updated.
b. Skill Assessments (Practical Performance)
- Skill Area: A list of key practical skills assessed (e.g., Cutting, Bending, Welding, Assembly, Blueprint Reading).
- Assessment Criteria: Clear criteria that describe the expectations for each skill area (e.g., “Ability to cut metal with precise measurements,” “Demonstrates proper welding technique”).
- Performance Rating: A scale to rate the student’s performance in each skill area (e.g., 1 to 5 scale, or Excellent, Good, Needs Improvement).
- Observation Notes: Instructor’s notes on the student’s performance, including specific examples or areas where improvement is needed.
- Skill Mastery: A statement indicating whether the student has mastered the skill or requires further practice.
c. Theoretical Knowledge Assessments
- Theory Topics: A list of the theoretical topics covered in the course (e.g., Metal Properties, Safety Protocols, Fabrication Processes, Welding Techniques).
- Assessment Method: The method used to evaluate theoretical understanding (e.g., written tests, quizzes, oral exams).
- Test Results: The student’s score or assessment outcome (e.g., percentage score or grade).
- Knowledge Application: A note on how well the student applies theoretical knowledge to practical tasks.
d. Safety and Compliance
- Safety Protocols Followed: Evaluation of how well the student adheres to safety standards in the workshop (e.g., use of PPE, adherence to safety procedures, use of equipment safely).
- Safety Incidents: Any incidents (if applicable), such as near misses or unsafe behaviors, and how they were handled or corrected.
- Safety Training Participation: A record of the student’s participation in safety drills or emergency response training.
e. Personal and Professional Development
- Work Ethic and Attitude: An assessment of the student’s approach to learning, including punctuality, attendance, teamwork, and initiative.
- Communication Skills: Evaluation of the student’s ability to communicate effectively with peers and instructors (e.g., listening skills, clarity in explaining ideas, asking for help).
- Problem Solving: An assessment of the student’s ability to handle challenges and troubleshoot problems in fabrication tasks.
- Time Management: Evaluation of the student’s ability to manage time and complete tasks within deadlines.
f. Feedback and Recommendations
- Instructor Feedback: Constructive feedback on the student’s performance, highlighting strengths and areas for improvement. This section should also encourage continued development in specific skills.
- Action Plan for Improvement: A tailored plan or set of recommendations for the student to improve certain skills, knowledge areas, or behaviors (e.g., “Practice welding techniques on scrap metal,” “Review theory on metal properties”).
- Additional Support Needed: If applicable, recommendations for additional resources, mentoring, or tutoring.
g. Final Assessment and Comments
- Final Grade/Rating: A final evaluation of the student’s overall performance (e.g., Pass/Fail, Grade).
- Instructor Comments: Overall assessment of the student’s progress, including an evaluation of their readiness for certification or future work in the field.
- Next Steps: Indication of what the student should focus on moving forward (e.g., “Attend advanced welding class,” “Prepare for final certification exam”).
3. Example of a Student Progress Report
Field Details Student Name Jane Smith Student ID 2345 Course Name/ID Sheet Metal Fabrication 101 Instructor Name John Doe Report Date 2025-03-31 Skill Assessments Cutting: 4/5 – Performs cutting with precision, slight irregularities. Bending: 5/5 – Perfect bends, follows safety protocols. Welding: 3/5 – Needs practice with steady hand and control. Theoretical Knowledge Metal Properties: 90% (Good understanding of metals) Safety Protocols: 95% (Excellent knowledge of PPE use) Fabrication Processes: 85% (Good understanding, needs review on blueprint reading) Safety and Compliance Safety Protocols Followed: Excellent adherence to safety measures. Safety Incidents: None Personal Development Work Ethic: Excellent; highly motivated and focused. Communication: Effective; clear communication with peers and instructors. Feedback and Recommendations Feedback: Excellent performance overall, with improvement needed in welding technique. Recommendations: Focus on improving welding control; practice on scrap metal. Final Assessment Final Grade: Pass Instructor Comments: Jane shows great promise in sheet metal fabrication. Consistent practice and focus on welding will improve her skills significantly. Next Steps: Prepare for final exam; attend advanced welding workshop. 4. Maintaining Student Progress Reports
a. Regular Updates
- Bi-weekly or Monthly Reports: Progress reports should be updated regularly (e.g., every two weeks or once a month) to track ongoing performance.
- End-of-Module/Term Report: A comprehensive report should be created at the end of each module or term, summarizing the student’s overall performance and achievements.
b. Record Keeping
- Digital Records: Maintain electronic copies of all reports in a secure, easily accessible system (e.g., using a Learning Management System (LMS) or Google Drive/Docs).
- Physical Copies: If required, provide printed copies of reports for students, with an additional copy kept in the student’s file for future reference.
c. Student Access
- Students should be provided with access to their progress reports regularly, allowing them to track their own performance and identify areas for improvement.
5. Benefits of Student Progress Reports
- Clear Tracking: Helps students and instructors keep track of skill development, attendance, and academic performance.
- Constructive Feedback: Provides a platform for students to receive regular feedback on their strengths and weaknesses.
- Motivation: Encourages students to stay focused and improve their performance through actionable recommendations.
- Certification Readiness: Ensures that students are meeting the necessary standards for certification or graduation.
Conclusion
SayPro Student Progress Reports are essential tools for monitoring and supporting students’ growth in the Sheet Metal Fabrication Program. By tracking both practical skills and theoretical knowledge, providing actionable feedback, and setting clear expectations, instructors can ensure that students are well-prepared for certification and future employment opportunities.
SayPro Equipment Maintenance Logs: A record of equipment inspections, repairs, and maintenance performed on the tools and machines used in training.
SayPro Equipment Maintenance Logs: Record of Inspections, Repairs, and Maintenance
To ensure that the tools and machines used in the SayPro Sheet Metal Fabrication Program are always in good working condition and meet safety standards, it’s essential to maintain comprehensive equipment maintenance logs. These logs will track the inspections, repairs, and routine maintenance performed on each piece of equipment used in training.
1. Purpose of Equipment Maintenance Logs
- Safety: Regular maintenance ensures that equipment is functioning safely, reducing the risk of accidents or malfunctions during training.
- Operational Efficiency: Well-maintained equipment operates efficiently, minimizing downtime and ensuring effective training sessions.
- Compliance: Keeping detailed records helps ensure that the equipment complies with safety regulations and industry standards.
- Cost Management: By tracking equipment issues early, maintenance logs help avoid costly repairs by addressing problems at the right time.
2. Components of the Equipment Maintenance Log
Each maintenance log should contain detailed information about the inspections, repairs, and maintenance activities conducted. Below is a breakdown of the essential components:
a. Equipment Information
- Equipment Name/ID: The name of the tool or machine (e.g., “MIG Welder”, “CNC Plasma Cutter”).
- Equipment Type: Category of equipment (e.g., cutting, bending, welding, etc.).
- Serial Number: Unique serial number for the equipment (if applicable).
- Manufacturer/Model: Manufacturer’s name and model number.
- Location: The workshop or area where the equipment is located.
b. Inspection Records
- Inspection Date: The date the equipment was inspected.
- Inspector Name: The name of the person performing the inspection (typically a technician, supervisor, or instructor).
- Inspection Checklist: A list of key components or systems that need to be checked (e.g., electrical components, safety features, calibration, cleanliness, etc.).
- Condition: A note on the equipment’s condition (e.g., “In good working condition,” “Requires minor repairs,” “Needs immediate attention”).
- Recommendations: Any recommendations for repairs, parts replacement, or maintenance that need to be addressed.
c. Maintenance and Repair Records
- Maintenance Date: The date when maintenance or repairs were performed.
- Description of Work: Detailed description of the maintenance or repair performed (e.g., “Replaced welding torch head,” “Lubricated bending press,” “Calibrated cutting machine”).
- Parts Replaced: Any parts that were replaced during maintenance (e.g., “Welding electrode,” “Pressure gauge,” “Cooling fan”).
- Service Provider/Technician Name: The technician or service provider who performed the repair or maintenance.
- Cost of Repairs: If applicable, the cost of the repair or part replacement.
- Equipment Downtime: Record of how long the equipment was out of service for maintenance or repairs.
- Follow-up Actions: Any follow-up actions required (e.g., “Monitor performance for the next week,” “Schedule next inspection in 3 months”).
d. Safety and Calibration Checks
- Calibration Date: Date of the most recent calibration check (especially important for machines that require precise measurements or settings).
- Calibration Results: Any issues found with calibration (e.g., “Out of specification, needs recalibration”).
- Safety Features Check: Notes on the inspection of safety features such as emergency stop buttons, safety guards, fume extraction systems, etc.
- Safety Concerns: Any identified safety concerns that need immediate attention (e.g., “Welding machine guard not functioning correctly”).
e. Next Scheduled Maintenance/Inspection
- Next Inspection Date: The scheduled date for the next inspection.
- Next Maintenance Date: If applicable, the next maintenance or calibration due date.
3. Example of an Equipment Maintenance Log Entry
Field Details Equipment Name/ID MIG Welder 3000 Equipment Type Welding Serial Number 1234567890 Manufacturer/Model SayPro / MIG-3000 Location Workshop 2 Inspection Date 2025-03-15 Inspector Name John Doe Inspection Checklist – Electrical system\n- Gas flow\n- Welding torch\n- Safety switch Condition Good working condition, minor wear on gas hose Recommendations Replace gas hose within 6 months Maintenance Date 2025-03-16 Description of Work Replaced welding torch tip, cleaned electrical contacts Parts Replaced Welding Torch Tip (Part #98765) Service Provider Name SayPro Technician (Jane Smith) Cost of Repairs $25.00 Equipment Downtime 1 hour Follow-up Actions None Calibration Date 2025-02-10 Calibration Results Calibrated, all parameters within specification Safety Features Check Checked emergency stop, all systems functioning properly Safety Concerns None Next Inspection Date 2025-06-15 Next Maintenance Date 2025-09-16 4. How to Maintain Equipment Logs
a. Physical or Digital Logs
- Physical Logs: Use a hard copy maintenance logbook for each piece of equipment, and ensure that it is stored in an easily accessible location.
- Digital Logs: Utilize a digital maintenance tracking system or spreadsheet (e.g., Microsoft Excel, Google Sheets, or specialized software like CMMS—Computerized Maintenance Management System).
- Digital logs allow easier tracking, filtering, and generating reports.
- Cloud-based systems ensure records are backed up and can be accessed remotely by authorized personnel.
b. Regular Updates
- Update the maintenance logs immediately after any inspection, maintenance, or repair is performed.
- Make sure to review logs regularly to identify recurring issues with specific equipment, which may indicate the need for more substantial repairs or replacement.
c. Integration with Inventory Management
- Maintain a linked inventory system to track spare parts used for repairs (e.g., welding tips, fuses, cutting blades). This helps ensure that necessary parts are available when needed and reduces downtime due to part shortages.
5. Benefits of Regular Equipment Maintenance Logs
- Improved Safety: Regular inspections and timely repairs ensure that all equipment is safe to use, reducing the risk of accidents.
- Increased Equipment Lifespan: Routine maintenance prevents wear and tear from turning into expensive repairs or replacements, extending the life of the tools and machines.
- Efficient Operations: Well-maintained equipment is more efficient and reliable, which helps maintain a consistent and productive training environment.
- Compliance and Reporting: Maintains records that can be reviewed during safety audits or regulatory inspections, ensuring compliance with health and safety standards.
Conclusion
SayPro’s Equipment Maintenance Logs are an essential tool for ensuring the safe and efficient operation of all tools and machinery used in the Sheet Metal Fabrication Program. By maintaining a comprehensive record of inspections, repairs, and maintenance, SayPro can ensure that equipment is always in top condition, students can learn in a safe environment, and the workshop can continue to operate effectively.
SayPro Instructor Certification: Proof of instructor qualifications, including certifications in sheet metal fabrication and any required training.
SayPro Instructor Certification: Proof of Instructor Qualifications
To ensure the highest standards of teaching and safety, it’s essential for SayPro instructors to have the appropriate qualifications and certifications. The following outlines the necessary certification and training requirements for instructors in the Sheet Metal Fabrication Program.
1. Required Qualifications for Instructors
a. Industry Experience
- Minimum Experience: Instructors should have at least 5 years of hands-on experience in sheet metal fabrication or a related field (e.g., welding, metalworking).
- Experience with Tools and Equipment: Instructors should be proficient in using all tools and equipment related to sheet metal fabrication, including cutting tools, welding machines, bending presses, and safety equipment.
- Experience in Supervision: Instructors should have prior experience supervising or training apprentices, trainees, or students in a workshop setting.
b. Educational Background
- Minimum Educational Requirements: A high school diploma or equivalent is required, with preference given to candidates who have completed post-secondary education in a related field (e.g., vocational school or technical college specializing in metalworking, welding, or fabrication).
- Relevant Certifications: Instructors should hold industry-recognized certifications in sheet metal fabrication and welding.
2. Certifications for Instructors
a. Sheet Metal Fabrication Certification
- SayPro Certification in Sheet Metal Fabrication
- This is a certification issued by SayPro that verifies the instructor’s proficiency in sheet metal fabrication.
- The certification is awarded upon successful completion of an internal SayPro training program and practical assessment in sheet metal fabrication skills.
- Industry-recognized Certifications (e.g., from institutions like the American Welding Society (AWS) or similar organizations)
- AWS Certified Welder: Certification demonstrating proficiency in welding (essential if the instructor will be teaching welding techniques as part of the curriculum).
- OSHA (Occupational Safety and Health Administration) Certification: Certification in workplace safety, ensuring instructors are familiar with workplace safety protocols and hazardous materials handling.
- Fabrication Certifications: Depending on the focus of the training, certifications such as the Fabricator’s Certification Program (FCP) may be required.
- National or International Fabrication Credentials
- National Institute for Metalworking Skills (NIMS) Certification: For instructors in the United States, a NIMS certification verifies expertise in manufacturing and metalworking processes.
- International Welding Inspector (IWI) Certification: For instructors teaching welding inspection, an IWI certification ensures the instructor has the required expertise in quality control and safety within the fabrication industry.
b. Teaching and Training Qualifications
- Vocational Training Certification
- Instructors should hold a Vocational Education and Training (VET) certificate or equivalent teaching qualification to ensure they have a solid understanding of adult learning principles and instructional design.
- Instructor Development Program:
- Instructors must complete a SayPro Instructor Development Program. This program includes training in:
- Effective Teaching Methods: How to convey technical material clearly and interactively.
- Classroom Management: Best practices for maintaining discipline and fostering a positive learning environment.
- Assessment Techniques: Understanding how to assess student performance, both practically and theoretically.
- Instructors must complete a SayPro Instructor Development Program. This program includes training in:
- Safety and Emergency Response Training
- Instructors must be certified in safety protocols specific to sheet metal fabrication, welding, and the operation of associated machinery.
- First Aid/CPR: Certification in First Aid and CPR is mandatory for all instructors to ensure immediate response in case of medical emergencies.
- Fire Safety Training: Instructors must undergo fire safety training and be able to conduct fire drills and manage fire-related emergencies in the fabrication workshop.
3. Continuous Professional Development (CPD)
To maintain their qualifications and ensure they are up-to-date with the latest industry standards and best practices, SayPro instructors must undergo Continuous Professional Development (CPD). This may include:
- Regular Industry Workshops and Conferences:
- Instructors are encouraged to attend workshops, seminars, and conferences related to sheet metal fabrication, welding, and manufacturing technologies.
- Annual Recertification and Assessment:
- Instructors should participate in annual performance reviews and complete refresher courses in relevant fabrication techniques, safety protocols, and teaching methods.
- Skills Upgrade:
- Instructors should be encouraged to take advanced certification courses to enhance their knowledge and qualifications in specific areas of sheet metal fabrication (e.g., advanced welding techniques, CAD for fabrication).
4. Documentation for Certification
To verify instructor qualifications and ensure compliance with industry standards, the following documentation should be provided for each instructor:
a. Proof of Education and Experience
- Copies of educational transcripts or diplomas.
- Detailed resume showcasing relevant work experience in sheet metal fabrication, welding, and teaching.
b. Copies of Certifications
- Sheet Metal Fabrication Certification (e.g., SayPro or industry-recognized certifications).
- Welding Certifications (AWS or other recognized welding certifying bodies).
- Safety and First Aid Certifications (e.g., OSHA, CPR, Fire Safety).
- Teaching Certification or Instructor Development Program Completion.
c. Training and CPD Records
- Records of completed workshops, conferences, and any ongoing professional development activities.
- Certificates of participation in refresher training and annual assessments.
d. Instructor Evaluation Reports
- Documentation of performance evaluations and feedback from students to assess teaching effectiveness and compliance with SayPro’s standards.
5. Instructor Certification Process
a. Instructor Selection
- Screening: Prospective instructors are vetted based on their qualifications, experience, and certification status.
- Interview and Practical Assessment: Conduct interviews and practical assessments to gauge teaching ability and technical proficiency.
b. Certification Issuance
- Once instructors meet all the certification and training requirements, SayPro issues an Instructor Certification that is valid for a specific period (e.g., 2 years), after which recertification is required.
c. Ongoing Monitoring and Support
- Observation and Mentorship: New instructors may be paired with experienced mentors who guide them through their initial teaching period.
- Regular Performance Reviews: Conduct bi-annual or annual reviews to assess teaching effectiveness, safety compliance, and student feedback.
Conclusion
The SayPro Instructor Certification program ensures that all instructors are qualified and prepared to provide high-quality training in sheet metal fabrication. With a combination of industry certifications, teaching qualifications, and continuous professional development, SayPro instructors are equipped to deliver comprehensive, safe, and effective instruction to students, helping them excel in the field of sheet metal fabrication.
SayPro Safety Protocols and Training Materials: Documentation covering safety measures, PPE requirements, and emergency procedures.
SayPro Safety Protocols and Training Materials
Safety is a crucial aspect of any training program, particularly in hands-on industries like sheet metal fabrication. To ensure the well-being of students and instructors, it’s essential to establish and maintain clear safety protocols and provide training materials that cover safety measures, Personal Protective Equipment (PPE) requirements, and emergency procedures. Below is a comprehensive guide for SayPro’s safety protocols and training materials for the Sheet Metal Fabrication Program.
1. Safety Protocols
a. General Safety Measures
- Training Requirement
- All students and instructors must undergo safety training before participating in any practical sessions.
- A safety orientation session should be conducted on the first day of the course, covering basic safety practices, emergency procedures, and PPE requirements.
- Work Area Safety
- Keep all work areas clean and free of debris.
- Mark hazardous areas with appropriate signage (e.g., wet floors, high-voltage areas).
- Ensure good lighting and ventilation in all work areas, especially for tasks that involve welding or cutting.
- Tool and Equipment Safety
- Inspect all tools and equipment for damage before use.
- Report any faulty or broken tools to the instructor immediately.
- Ensure all tools are stored properly when not in use to prevent accidents.
- Posture and Ergonomics
- Encourage proper lifting techniques for heavy materials and tools.
- Provide workstations that accommodate good posture to minimize strain during tasks like welding or bending metal.
b. Personal Protective Equipment (PPE)
PPE is critical for preventing injuries and protecting workers from hazards such as flying metal, burns, and fumes. Below is a list of PPE required for different tasks in the sheet metal fabrication workshop.
- Head Protection
- Welding helmet: Required when using welding equipment to protect against sparks, UV radiation, and bright light.
- Hard hats: Worn in areas where there is a risk of falling objects (e.g., from overhead shelves or machinery).
- Eye Protection
- Safety goggles or glasses: Must be worn when cutting, grinding, or performing any tasks where debris or metal fragments may fly.
- Face shields: Used for welding to protect the face from sparks and intense light.
- Hand Protection
- Leather gloves: Worn when handling sheet metal to avoid cuts, abrasions, and burns.
- Welding gloves: Made of heat-resistant material to protect hands when welding.
- Body Protection
- Flame-resistant coveralls: Worn when welding, cutting, or grinding to protect the body from sparks, heat, and sharp metal edges.
- Long sleeves and pants: Necessary to prevent burns and cuts. Ensure clothing is tight-fitting to avoid entanglement with machinery.
- High-visibility vests: To be worn in areas with heavy machinery or vehicles moving in and out of the work area.
- Foot Protection
- Steel-toed boots: Worn to protect the feet from heavy objects falling or metal debris.
- Slip-resistant soles: Ensure boots have slip-resistant soles for safety in wet or oily environments.
- Respiratory Protection
- Dust masks or respirators: Worn during operations that produce dust or fumes, such as grinding, cutting, or welding.
- Fume extractors: Ensure fume extractors are used during welding and cutting processes to remove hazardous fumes from the air.
- Hearing Protection
- Earplugs or earmuffs: Used when working with noisy equipment like grinders, presses, or cutting tools.
2. Emergency Procedures
a. Fire Safety
- Fire Extinguishers
- Fire extinguishers should be placed near each welding and cutting area.
- Ensure instructors and students are trained in the use of fire extinguishers (i.e., PASS method: Pull, Aim, Squeeze, Sweep).
- Fire Blanket
- A fire blanket should be readily available in case of small fires, especially in welding or cutting areas.
- Fire Evacuation Plan
- Post evacuation routes clearly around the workshop.
- Conduct fire drills regularly to ensure everyone knows how to evacuate quickly and safely in the event of a fire.
b. First Aid and Medical Emergencies
- First Aid Kits
- First aid kits should be stocked and accessible in every work area.
- The kit must contain basic supplies such as bandages, antiseptics, burn cream, eye wash, and splints.
- Minor Injuries
- For small cuts, abrasions, and burns, apply first aid and refer to the instructor for further guidance.
- For eye injuries, immediately flush the eye with water using an eyewash station and seek medical attention.
- Severe Injuries
- In case of major injuries (e.g., deep cuts, burns, fractures), call emergency services immediately and do not attempt to move the injured person unless necessary.
- Provide basic first aid while waiting for professional medical assistance (e.g., apply pressure to a bleeding wound).
- Emergency Contact Information
- Display emergency phone numbers and contacts in a visible location within the workshop area.
c. Emergency Shutoff and Equipment Lockout
- Emergency Shutoff Procedure
- Emergency stop buttons or switches must be clearly labeled and accessible for each major piece of equipment.
- All instructors and students should be trained on how to immediately shut down equipment in case of malfunction or emergency.
- Lockout/Tagout (LOTO) Procedures
- Implement a Lockout/Tagout program to ensure machinery is properly shut down and cannot be turned on while being repaired or maintained.
- Only qualified personnel should perform lockout/tagout procedures, ensuring that all energy sources are fully isolated.
3. Safety Protocols Training Materials
a. Safety Manual
The SayPro Safety Manual should include all safety protocols, PPE requirements, and emergency procedures in a clear and concise format. It should be provided to each student at the beginning of the course and should include:
- Introduction to workshop safety
- Detailed PPE requirements for different tasks
- Step-by-step emergency procedures (fire, medical, equipment failure)
- Signage and hazard identification guide
b. Safety Training Presentation
A PowerPoint presentation or interactive training video should be used to reinforce safety procedures:
- PPE demonstration: Show examples of the proper and improper use of PPE.
- Tool and equipment safety: Demonstrate how to operate equipment safely and correctly.
- Emergency procedures: Walk through how to react in case of different emergencies (e.g., fire, injury, tool malfunction).
c. Hands-on Safety Training
- Conduct hands-on safety drills where students practice using fire extinguishers, first aid kits, and the emergency shutdown procedures.
- Provide regular mock emergency scenarios where students must demonstrate their ability to follow emergency protocols.
d. Safety Quiz and Certification
At the end of the safety training session, have students complete a safety quiz to ensure they understand the protocols.
- The quiz should cover:
- Proper use of PPE
- Fire and emergency evacuation procedures
- First aid basics
- Emergency shut-off protocols
- Issue a Safety Certificate to students who successfully complete the quiz, demonstrating their commitment to safety.
4. Continuous Safety Monitoring
- Regular Safety Audits: Conduct monthly safety audits to check that safety protocols are being followed and equipment is maintained.
- Instructor Refresher Courses: Instructors should attend periodic refresher courses to stay updated on safety regulations and best practices.
- Student Feedback: Encourage students to provide feedback on safety concerns, which can be used to improve safety procedures and practices.
Conclusion
A thorough safety training program and clear safety protocols are essential for maintaining a safe and productive environment in the SayPro Sheet Metal Fabrication Program. By ensuring that students are well-versed in PPE usage, emergency procedures, and tool safety, SayPro can minimize accidents and create a safe learning atmosphere. Regular training, hands-on drills, and continuous monitoring will ensure a strong safety culture throughout the program.
- Training Requirement
SayPro Course Curriculum: Detailed outlines and lesson plans for each aspect of the course, including theoretical and practical sessions.
SayPro Course Curriculum: Detailed Outlines and Lesson Plans
Creating a well-structured course curriculum with detailed outlines and lesson plans is crucial for ensuring the program effectively covers all aspects of sheet metal fabrication. This includes both theoretical knowledge (such as understanding metal properties, safety protocols, and fabrication techniques) and practical sessions (like cutting, bending, welding, and finishing). Below is a detailed outline for SayPro’s course curriculum.
1. Course Overview
Course Title: Sheet Metal Fabrication
Duration: X weeks (e.g., 12 weeks)
Mode of Delivery: Combination of theoretical sessions and hands-on practical sessions
Target Audience: Beginner to intermediate learners interested in sheet metal fabrication
Certification: Upon completion of the course, students will receive a SayPro Certification in Sheet Metal Fabrication.2. Theoretical Sessions
a. Module 1: Introduction to Sheet Metal Fabrication
Objective: Provide foundational knowledge of sheet metal fabrication and introduce the tools and equipment used.
Lesson Plan:
- Lesson 1.1: Introduction to Sheet Metal
- Definition and importance of sheet metal
- Types of metals used (steel, aluminum, copper, etc.)
- Metal gauges and thicknesses
- Lesson 1.2: Properties of Metals
- Strength, flexibility, malleability, and durability
- How to choose the right metal for a project
- Metallurgical processes (e.g., annealing, tempering)
- Lesson 1.3: Overview of Tools and Equipment
- Cutting tools: shears, saws, and plasma cutters
- Bending tools: brakes and presses
- Welding machines and tools: MIG, TIG, and Stick welding
Duration: 2 sessions (1 hour each)
b. Module 2: Metalworking Fundamentals
Objective: Build a deeper understanding of essential metalworking concepts like cutting, shaping, and joining metals.
Lesson Plan:
- Lesson 2.1: Measuring and Marking Techniques
- Importance of accuracy in fabrication
- Tools: calipers, tape measures, and templates
- Marking metal for cutting and bending
- Lesson 2.2: Cutting Techniques
- Manual cutting methods (e.g., hand shears, snips)
- Power cutting methods (e.g., band saw, laser cutting, plasma cutting)
- Lesson 2.3: Bending and Forming Techniques
- Different types of bends (e.g., V-bend, U-bend, corner bends)
- Using a bending brake, press brake, and roller
- Forming metal with hammers and anvils
Duration: 3 sessions (1 hour each)
c. Module 3: Welding and Joining Techniques
Objective: Introduce students to various welding methods and their applications.
Lesson Plan:
- Lesson 3.1: Introduction to Welding
- Overview of welding processes: MIG, TIG, Stick welding
- Safety protocols in welding (e.g., fire hazards, PPE)
- Differences between welding and brazing/soldering
- Lesson 3.2: MIG (Metal Inert Gas) Welding
- Setup and operation of MIG welders
- Techniques for creating strong, clean welds
- Practical tips for achieving optimal weld penetration
- Lesson 3.3: TIG (Tungsten Inert Gas) Welding
- Basics of TIG welding and when to use it
- Welding thin metals and achieving precise welds
- Advanced TIG techniques for different metal types
Duration: 4 sessions (1 hour each)
d. Module 4: Safety and Best Practices
Objective: Equip students with essential safety knowledge for working in a metal fabrication shop.
Lesson Plan:
- Lesson 4.1: Personal Protective Equipment (PPE)
- Types of PPE (e.g., gloves, goggles, face shields, welding helmets)
- Proper usage and care of PPE
- Lesson 4.2: Workshop Safety Protocols
- Safe operation of tools and machinery
- Handling hazardous materials and chemicals
- Fire safety and emergency protocols
- Lesson 4.3: Handling and Storing Metals Safely
- Storing sheet metal and tools in a safe manner
- Avoiding workplace accidents related to heavy lifting
Duration: 2 sessions (1 hour each)
3. Practical Sessions
a. Module 1: Basic Metalworking Skills
Objective: Enable students to apply their theoretical knowledge through hands-on practice with metalworking tools.
Lesson Plan:
- Lesson 1.1: Practical Cutting Techniques
- Students practice cutting sheet metal using shears and power tools.
- Focus on precision and maintaining clean, straight cuts.
- Lesson 1.2: Basic Bending Techniques
- Practice bending metal to specified angles using a manual bending brake.
- Apply proper techniques for creating different bend types.
- Lesson 1.3: Basic Shaping Techniques
- Use hammers and anvils to shape sheet metal.
- Practice creating simple curved shapes and smooth finishes.
Duration: 3 sessions (2 hours each)
b. Module 2: Welding and Joining
Objective: Teach students how to weld and join metal components.
Lesson Plan:
- Lesson 2.1: Introduction to MIG Welding
- Students practice setting up and operating a MIG welder.
- Focus on creating smooth, consistent welds on thin sheet metal.
- Lesson 2.2: Introduction to TIG Welding
- Students set up and operate a TIG welder for precision work.
- Focus on welding thin metals with clean and precise joints.
- Lesson 2.3: Joining Metal Parts
- Students learn to join fabricated metal parts together using various methods (e.g., bolts, welds, rivets).
- Focus on structural integrity and alignment.
Duration: 4 sessions (2 hours each)
c. Module 3: Advanced Fabrication Projects
Objective: Students will work on real-world fabrication projects to showcase their learned skills.
Lesson Plan:
- Lesson 3.1: Designing Fabrication Projects
- Students choose or are assigned a fabrication project (e.g., a metal frame, tool rack, small structure).
- Create designs and develop technical drawings using basic CAD software or hand sketches.
- Lesson 3.2: Project Execution
- Students fabricate the designed project, applying cutting, welding, and bending techniques.
- Emphasis on teamwork, quality control, and precision in project execution.
- Lesson 3.3: Finishing and Inspection
- Students apply finishing techniques such as grinding, polishing, and painting.
- Conduct inspections to ensure the project meets design specifications.
Duration: 4 sessions (2 hours each)
4. Evaluation and Feedback
a. Theoretical Assessments
- Quizzes or exams covering theoretical topics such as metal properties, welding techniques, and safety protocols.
- Assignments to reinforce understanding of course material.
b. Practical Assessments
- Observation and assessment of students during hands-on sessions.
- Completion of individual or group projects, which are evaluated for quality, precision, and safety.
- Practical tests on using equipment (e.g., MIG welding test, bending test).
5. Final Project and Certification
Objective: Provide students with an opportunity to demonstrate their full range of skills by completing a final project.
Lesson Plan:
- Students design and fabricate a project of their choice or given project criteria.
- Upon successful completion and presentation of the final project, students will receive their certification.
Duration: 2 sessions (3 hours each)
Conclusion
By dividing the curriculum into theoretical modules and practical sessions, SayPro ensures that students not only gain knowledge but also develop the hands-on skills necessary for success in sheet metal fabrication. Through continuous evaluation and feedback, learners can track their progress and improve their performance, ensuring they are fully prepared to enter the workforce or pursue further specialization in the field.
- Lesson 1.1: Introduction to Sheet Metal
Saypro Documentation Ensure all required certifications, permits, and other paperwork are completed as per SayPro’s standards.
SayPro Documentation: Ensuring Certifications, Permits, and Other Paperwork Are Completed as Per SayPro’s Standards
Proper documentation of certifications, permits, and other essential paperwork is crucial for compliance, student success, and program credibility. For SayPro’s Sheet Metal Fabrication Program, this includes making sure all required documentation is completed in line with both industry standards and regulatory requirements. Below is a comprehensive guide on how to ensure all necessary paperwork is handled effectively:
1. Certification Documentation
a. Tracking Student Certifications
Certification is an important milestone in the training process, particularly in technical programs like sheet metal fabrication. Students must receive appropriate certification upon completing certain training modules or the entire program.
What to include in certification records:
- Certification issued: Record the type of certification issued (e.g., completion certificates, competency-based certifications).
- Student details: Include the student’s full name, registration number, and contact information.
- Course details: Document the course/module for which certification is granted, including dates of completion.
- Certification authority: Note who issued the certification (e.g., SayPro, an accredited certifying body, industry associations).
- Expiration dates: If applicable, record the expiration date of certifications (e.g., some safety certifications may require renewal after a certain period).
How to maintain certification records:
- Digital storage: Use a student management system to store and track student certifications, making it easy to retrieve and update records.
- Physical copies: Maintain physical files for certification records in a secure, organized manner, especially for certifications that need to be shown to regulatory authorities or industry stakeholders.
b. Verification of Certification
Ensure that students’ certifications are verifiable by accrediting bodies or relevant authorities.
What to include:
- Accreditation number: Document the accreditation number or registration number for each certification for verifiable tracking.
- Verification contact: Include the contact details of the certifying authority for third-party verification.
- Certification guidelines: Keep a reference copy of the guidelines and requirements for each certification to ensure proper issuance.
2. Permits and Licenses Documentation
a. Required Permits for Operations
Certain types of work (especially when using specific equipment or working with hazardous materials) may require permits or licenses. This is particularly relevant for sheet metal fabrication in areas like welding, cutting, and working with industrial machinery.
What to include in permit documentation:
- Permit type: Identify the specific permits required for operations (e.g., welding permits, equipment usage permits).
- Permit holders: Ensure that only qualified personnel and students are issued the necessary permits. Keep records of who holds each permit.
- Permit validity: Document the issue and expiration dates for permits, and schedule renewals as needed.
- Regulatory body: Include the name of the regulatory authority that issues the permit (e.g., local government bodies, occupational safety organizations).
b. Equipment Operation Licenses
For specific machinery (such as bending presses or welding machines), students or instructors may require licenses to operate them.
What to include in equipment operation license records:
- License details: Document the license type (e.g., welding machine operator license, heavy equipment operation license).
- Issued to: Keep a record of the individual to whom the license was issued.
- License validity: Track the start and expiration dates of the license and initiate renewal processes before expiry.
- Re-certification: If necessary, document when re-certification or additional training is required.
3. Health and Safety Paperwork
a. Safety Training Certifications
In any technical training program, especially in fabrication, safety is paramount. This includes certifications for personal protective equipment (PPE) usage, first-aid training, and hazardous material handling.
What to include in safety training records:
- Type of training: Document the specific safety courses completed (e.g., general fabrication safety, first-aid, welding safety).
- Date of completion: Include the date when each training session was completed.
- Instructor details: Record the name of the instructor or trainer who conducted the safety training.
- Certification: Ensure that students receive proper certificates upon completing safety training, and document these certificates in the student records.
b. Incident and Accident Reports
Document any safety incidents or accidents that occur during training. This will not only help in improving safety protocols but also ensures compliance with industry and regulatory standards.
What to include in incident reports:
- Incident details: Record the date, time, and location of the incident.
- Description of incident: Provide a detailed description of what occurred, including any injuries or damages.
- Corrective action: Document the corrective action taken, including changes to training, equipment maintenance, or safety procedures.
- Follow-up: Ensure a follow-up process is in place to check that corrective actions have been effective.
4. Compliance with Industry and Regulatory Standards
a. Regulatory Compliance
Ensure that all documentation complies with industry standards (e.g., ISO certifications, national safety standards) and local regulations.
What to include:
- Standards adherence: Regularly review industry standards (e.g., ISO 9001, ISO 45001 for occupational health and safety) to ensure SayPro is aligned with the latest regulations.
- Compliance audits: Periodically conduct compliance audits to ensure that SayPro is meeting all regulatory requirements for the training program and safety standards.
- Audit trails: Keep records of audits, their findings, and any corrective measures taken in response.
b. Program Accreditation
Ensure that SayPro’s sheet metal fabrication program is properly accredited by relevant training and certification bodies. This will enhance the program’s credibility and ensure it meets established standards.
What to include:
- Accreditation body: Document the name and accreditation number of the organization that accredits the program.
- Accreditation renewal: Keep track of the renewal dates and procedures for maintaining the program’s accreditation status.
- Compliance certifications: Maintain copies of certifications and records from accrediting bodies that show SayPro is compliant with industry and educational standards.
5. Student Enrollment and Attendance Records
a. Enrollment Documentation
Maintaining accurate student enrollment records is essential for compliance with regulatory requirements and for tracking student progress throughout the program.
What to include:
- Enrollment forms: Keep completed enrollment forms, including personal information, emergency contacts, and consent forms.
- Course registration: Record the specific courses or modules each student has registered for.
- Start and end dates: Document the enrollment period, including the start and end dates of each student’s program.
b. Attendance Tracking
Track attendance to ensure that students meet the required attendance hours for certification.
What to include:
- Attendance sheets: Keep records of daily attendance, noting any absences.
- Absence explanations: Document explanations for absences (e.g., medical leave) and any actions taken (e.g., makeup sessions).
6. Record Retention and Security
a. Long-Term Record Retention
Some records, particularly certifications and safety incident reports, must be kept for a long period, as required by industry regulations.
What to include:
- Retention periods: Follow legal and regulatory requirements for how long various types of documents must be kept. For example, student records may need to be retained for 5 to 10 years.
- Archiving: Use secure storage systems, both digital and physical, to ensure that records are easily accessible but also protected from unauthorized access.
b. Secure Access Control
Ensure that sensitive documentation, such as student records and safety reports, is accessible only to authorized personnel.
How to ensure security:
- Password protection: Use strong passwords and encrypted storage for digital records.
- Physical security: For physical records, store them in locked cabinets or secure rooms, with restricted access to authorized staff only.
Conclusion: Effective Documentation for Program Integrity and Compliance
Properly maintaining documentation for certifications, permits, safety paperwork, and other essential records is vital to the success and compliance of the SayPro Sheet Metal Fabrication Program. By ensuring all required paperwork is completed, stored securely, and easily accessible, SayPro can maintain its credibility, improve its program quality, and ensure regulatory compliance.
SayPro Evaluation and Feedback: Provide constructive feedback and offer guidance for improvement where necessary.
SayPro Documentation: Maintaining Records of Student Progress, Course Materials, and Safety Incidents
Maintaining comprehensive documentation is a key element of any training program, including SayPro’s Sheet Metal Fabrication Program. It helps track student progress, ensures safety protocols are followed, and keeps records of course materials for future reference and program improvement.
Here’s a detailed breakdown of how to maintain records in each of these areas:
1. Student Progress Records
a. Tracking Academic and Practical Performance
Keeping accurate and up-to-date records of student progress allows instructors to monitor performance and provide personalized feedback. It also helps with assessing readiness for certification or graduation.
What to include in student progress records:
- Practical performance: Document each student’s skill development through hands-on assessments, noting areas of strength and areas needing improvement (e.g., welding accuracy, cutting precision).
- Theoretical knowledge: Record scores and feedback from written tests, quizzes, and assessments related to metal properties, safety, and welding techniques.
- Milestone achievements: Track specific milestones such as mastering certain skills (e.g., successfully welding a joint or cutting a specific metal) or completing certain course modules.
- Project completion: Maintain records of student projects (e.g., finished structures, completed assignments) with timestamps to track progress over time.
How to organize student progress records:
- Digital records: Use a student management system (e.g., Learning Management System or LMS) to store progress data for easy retrieval and tracking.
- Physical portfolios: If digital tools are not available, maintain physical student portfolios that include assessments, feedback sheets, and project evaluations.
- Progress charts: Develop progress charts or score sheets for each student, where scores from practical and written assessments are recorded. This can be organized by tasks or course sections.
b. Regular Reviews
Schedule periodic reviews to assess overall student progress and discuss any challenges or adjustments needed for individual learners.
Example:
- Conduct mid-term reviews to evaluate if students are on track to meet course objectives and provide additional help where necessary.
- End-of-course evaluations to assess whether the students have successfully met the learning outcomes and are ready for certification.
2. Course Materials Documentation
a. Organizing and Updating Course Materials
It’s essential to maintain a well-organized repository for all course materials, including:
- Lesson plans: Document detailed lesson plans for each module, including theoretical content, practical exercises, and evaluation methods.
- Training manuals: Keep copies of up-to-date training materials, such as handbooks for sheet metal fabrication, safety guides, and equipment operation manuals.
- Multimedia resources: Store instructional videos, presentations, and any other multimedia resources that support learning.
- Assessment tools: Maintain copies of quizzes, exams, and rubrics used to evaluate student progress.
How to organize course materials:
- Digital repository: Store all course materials in a cloud-based system or an internal digital storage system so that they can be easily updated, accessed, and shared.
- Version control: Maintain records of revisions for each course material. As industry practices or safety regulations evolve, the course content should be updated, and keeping version history will ensure that instructors use the latest materials.
- Physical copies: If necessary, keep physical copies of important documents, especially safety manuals, which students should have access to during hands-on work.
b. Consistency and Accessibility
Ensure that all instructors have easy access to the materials they need to deliver lessons consistently. If the program has multiple instructors, a centralized system for sharing materials helps standardize instruction.
Example:
- A shared drive or system where lesson plans, assessments, and instructional videos are stored, allowing instructors to reference and update course materials as needed.
3. Safety Incident Records
a. Documenting Safety Incidents
Safety is a top priority in hands-on training environments like sheet metal fabrication. In the event of any safety incidents, thorough documentation is essential for future safety improvements and compliance with workplace safety standards.
What to include in safety incident records:
- Date and time: Record when the incident occurred.
- Incident details: Include a description of what happened, which equipment was involved, and any injuries or damage that resulted.
- Witnesses: Note any witnesses to the incident and their statements.
- Actions taken: Document any immediate corrective actions taken, such as providing medical care, stopping the operation, or replacing damaged equipment.
- Root cause analysis: Identify the cause of the incident (e.g., human error, equipment malfunction, improper use of PPE).
- Corrective measures: Detail the corrective or preventive measures put in place to avoid future incidents (e.g., additional training, equipment repairs, updated procedures).
b. Safety Incident Reports
Create safety incident report forms that must be completed for each safety-related event, no matter how minor. These reports should be reviewed regularly to identify patterns or recurring issues.
Example:
- Incident Report Form:
- Incident description.
- Safety measures in place at the time of the incident.
- Action plan to address the incident and prevent recurrence.
c. Safety Audits
In addition to incident reports, conduct regular safety audits to ensure that safety protocols are being followed and that there are no potential hazards in the training area.
What to include in safety audits:
- Equipment inspections: Regular checks of equipment to ensure they are functioning correctly and safely.
- Safety training compliance: Ensuring that all students and instructors are up-to-date with safety training and know how to use PPE and equipment correctly.
- Emergency procedures review: Confirm that emergency exits, fire extinguishers, first aid kits, and other safety features are in place and operational.
4. Archiving and Access Control
a. Long-Term Record Keeping
Some documents, especially those related to safety incidents and student certifications, must be kept for a long period for compliance, auditing, and future reference.
How to archive records:
- Digital storage: Use secure cloud storage or on-premise servers to store all records, ensuring that they are regularly backed up and protected from unauthorized access.
- Paper records: For physical documents, establish a system for organizing and storing them securely (e.g., filing cabinets, labeled folders) and maintaining easy access.
b. Data Protection and Access Control
Maintain confidentiality and data protection for student records, especially in compliance with privacy laws such as the Protection of Personal Information Act (POPIA) in South Africa. Set up access control protocols to ensure that only authorized personnel can view or modify sensitive records.
Example:
- Implement role-based access in a student management system to ensure that only instructors and administrators can access or update student records.
- Ensure physical safety incident records are stored in locked cabinets and only accessible to designated safety officers or senior instructors.
5. Regular Review and Updates
a. Program Review
Regularly review all documentation systems (student progress, course materials, and safety incident records) to ensure they are up-to-date and reflective of current best practices in the industry.
Example:
- Hold annual reviews of student progress records to ensure that evaluation methods align with industry standards.
- Update course materials and safety protocols as new technologies or safety regulations emerge in the field of sheet metal fabrication.
b. Feedback Loops
Gather feedback from instructors, students, and safety officers to improve documentation processes and make necessary adjustments. This feedback can help refine safety protocols, teaching methods, and record-keeping procedures.
Conclusion: Effective Documentation for Program Success
Proper documentation of student progress, course materials, and safety incidents is vital for maintaining a high-quality and safe training environment. By keeping clear, accurate, and up-to-date records, SayPro can ensure that students are progressing effectively, that safety standards are adhered to, and that the training program is constantly evolving in response to feedback and industry changes.